Owners of property next to the ocean often require marine contractors to build or repair docks, boat lifts and shoreline erosion control structures. Careful selection of a qualified contractor is critical to ensuring the success of such projects.
Marine software systems that provide real-time sensor data gathering, computation, display and logs are valuable tools for contractors. Such systems can help marine contractors get paid precisely for dredging work, reach project benchmarks and demonstrate compliance with regulations.
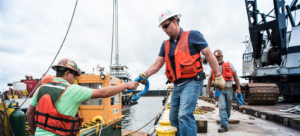
Marine contractors have the specialized construction knowledge and experience to build a wide range of structures, including docks, seawalls, marine piers, wharves, bulkheads, jetties and more. They also handle dredging, filling, shoreline erosion control and coastal restoration. Their work often involves high-level engineering and design technology, as well as specialized construction materials and equipment.
When choosing a marine contractor for your project, look for one with a solid reputation and track record of meeting deadlines. In addition, choose a company with stable management and long-tenured leaders. This will help you to avoid shady business practices and ensure that you get the quality work you need on time and within budget.
After the initial consultation, your marine contractor will prepare a proposal for the work that needs to be done. This may include sketches, plans or computer simulations to give you a clear idea of what your property will look like after the seawall has been completed. It will also specify the type of seawall that will be built (vertical, stepped or mound-type), and the material that will be used (concrete, stone or wood).
The proposal will then be presented to you for review and approval. If you have any questions or concerns, this is the time to voice them. Your marine contractor should be willing to address your concerns and explain any additional costs or delays that may arise.
Once the contract has been approved, the marine contractor will begin the construction process. This will include excavating the site, building the foundation and installing the seawall. Depending on the complexity of the project, this step may take several weeks or months.
During the construction phase, your marine contractor will monitor the project on a daily basis to make sure that it is progressing according to plan. They will also be responsible for obtaining any required permits from local authorities and other relevant government agencies. They will also handle the sand replacement, waterway openings and any other requirements related to your project.
Once the construction is complete, your seawall will be in place and ready to protect your property from erosion. However, it’s important to remember that even the best seawall is not a permanent solution to beach erosion. It’s still possible that your seawall will need to be repaired or replaced over time, particularly if it is located in an active erosion zone.
Dock Repairs
Most waterfront property owners will need the services of a marine contractor at one time or another, whether it’s to construct or repair a dock, boat house or ramp, seawall, cofferdam, or other shoreline erosion control structure. The selection of a reliable, knowledgeable and experienced marine contractor can mean the difference between a project done well and a botched job. Here are some tips, questions to ask and red flags to watch for when choosing a marine contractor for your next project.
Marine contractors should have skill and experience in the construction and repair of both residential and commercial waterfront structures. They should also have a solid understanding of building materials and environmental conditions. For example, it is important that wooden docks are constructed with pressure-treated wood meeting specific minimum standards. This is essential to the longevity and durability of the structure. Also, different mixtures of concrete are required in coastal environments compared to dry-land settings.
In addition to being able to perform the necessary work on your waterfront projects, a marine contractor should be able to work within your budget and provide you with a fair and reasonable estimate. They should also be able to answer any questions or concerns that you may have throughout the project.
When selecting a marine contractor for your next project, it’s important to take the time to find out if they have a solid track record and are licensed and insured. A good place to start is by searching the Internet and looking at local listings for marine contractors. It’s also a good idea to get recommendations from friends and neighbors who have used a marine contractor in the past.
A marine contractor bond is a type of surety bond that provides financial protection for clients in the event that the contractor fails to fulfill their contractual obligations or causes damage while working on a project. The bond is obtained through a licensed surety company and is often a requirement before beginning work on any waterfront project. In order to obtain a marine contractor bond, applicants must fulfill all bond requirements, including submitting the correct documents and paying their premium on time.
Boat Lifts
Having a boat lift installed at your dock allows you to store your watercraft safely out of the water when not in use. This not only protects the hull from damage, it also prevents marine growth and barnacles from attaching to the vessel, which significantly impacts resale value. Additionally, it takes away the need to trailer your boat to a public boat ramp, which can save you time and effort.
If you are considering the installation of a new boat lift, it is important to understand the different types available. First and foremost, it is essential to determine the type of lift that will be suitable for your vessel’s weight and size. The most accurate method of calculating this is by using the boat’s “dry” weight, which includes the weight of the vessel without fluids or accessories. This is usually included in the manufacturer specifications. However, you should also consider the “wet” weight of the vessel, which will include the weight of fuel, batteries, passengers and other accessories. Err on the high side when determining this to allow for a safety margin.
There are three main types of boat lifts, each of which is suited for a particular situation:
Bottom standing boat lifts (also known as freestanding boat lifts) typically consist of a set of two or more forklift-like arms that extend below the water and are powered by hydraulics. These lifts are ideal for situations where there is limited space or the water depth is shallow.
Pile mount or piling boat lifts are more permanent options that attach directly to a dock or a foundation of concrete or wood piles. This boat lift style is able to withstand significant water level changes and can support heavy, long boats with ease.
Finally, a floating boat lift is a good option for areas where the water level fluctuates significantly and is prone to tide shifts. Floating boat lifts are composed of air-filled chambers that float on the surface of the water and can accommodate vessels up to 45 feet in length. This type of lift is easy to maintain and can be expanded easily if necessary, making it an excellent choice for large watercrafts.
Boat Ramps
A boat ramp is a type of marine concrete structure for trailered small craft that provides easy access to waterways. The ramps have a sloping paved surface (typically one vertical: eight horizontal) that extends from the level of the land at the top down to a point below low tide where launching is possible. Boat ramps are often constructed using a mix of concrete elements, with in-situ concrete ground slabs used above the tidal zone and precast slabs used in the wet portion.
It is important to work with a Marine Contractor who has experience building boat ramps, and who understands the specific requirements of each location. It is not unusual for a local jurisdiction to have strict regulations for the design and construction of these types of structures.
In addition, marine contractors should have the expertise and experience to work within the guidelines of all relevant state and local permits. These documents may require detailed drawings, engineering studies, and/or environmental clearances. In addition, a thorough review of coastal erosion control publications should be reviewed to ensure the construction methods proposed by the contractor are consistent with accepted standards.
For example, it is common to see a pier with heavie cleats, and while they provide good traction for boats, these can also cause people to trip over them. Instead, a better option is to have a curb built on the pier, which provides a hand grip for boarding and disembarking the boat, as well as providing a place for the boater to tie their rope.
The ramp’s slope is another factor that must be considered, as it should be a relatively gentle angle to provide good vehicle traction and to avoid slipping and falls. A ramp that is too steep will create difficulty for drivers, particularly front-wheel drive vehicles, and a ramp that is too shallow will cause the boat to sink in the water when being loaded.
Lastly, it is very important that the ramp have good drainage. This can be achieved by incorporating a series of drainage grooves that are trowelled into the concrete surface. The sloping surfaces of the ramp should also be designed to deflect sediment from the site. This will not only reduce maintenance costs over time, but it will make the boater’s experience safer and more pleasant.